Femtosecond laser micromilling, or ablative laser processing, removes material in, virtually, any shape or pattern. Cut widths down to a few microns are achievable and sub-micron kerfs are possible for very thin materials. Femtosecond laser machining enables repeated manufacture of precision components with complex patterns. 3D blind features can be created with depth resolutions within a few percent of the feature depth and resolutions as high as a few 10’s of nanometers can be performed on production parts.
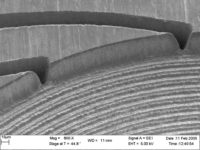
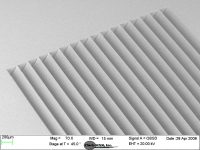
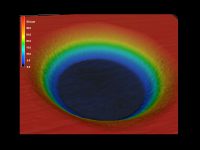
Serial Sectioning
Applying ablative, or subtractive, patterning processes to an entire material surface exposes underlying areas that can be examined and characterized using a variety of microscopic or spectroscopic analytical techniques. Repeating the process allows for 3D reconstruction of a sample often called serial sectioning or 3D Tomography.
Wear and Defect Simulation
Precision laser micromilling into pristine surfaces, with highly controlled dimensions, creates defect standards that can be used to calibrate test inspection equipment for critical components like ceramic ball bearings. Similarly, removing controlled amounts of materials from surfaces creates artificial wear for test parts in industries such as automotive and heavy equipment. The machined results can be processed on many materials including ceramics, metals, composites and exotic materials like diamond.
Clark-MXR Micromanufacturing – “Where your imagination of the very small is realized”
- Nanoscale to Macroscale manufacturing
- Femtosecond laser and mechanical machining
- SEM Inspection
- 3D Laser scanning microscope inspection
- Assembly, especially of small delicate components
- Cleaning
- Packaging, including Class 100 critical environment packaging
-
Plasma cleaning
-
Electro-polishing
-
Lapping
-
Micro-bead blasting